scara robot pdf
Compact high-performance SCARA robot with unique workspace design RS-SERIES SPECIFICATIONS RS3 RS4 Arm length 350 mm 550 mm Repeatability Joints 1 2 0010 mm 0015 mm Payload Rated 1 kg 1 kg Maximum 3 kg 4 kg Standard cycle time1034 sec 039 sec Installation environment Standard Cleanroom2 ESD Available controllers RC180 RC700A. These SCARA robots have undergone countless modifications in an ever changing marketplace and amassed a hefty record of successful products making them an essential part of the YAMAHA robot lineup.
Pdf Design Of An Economical Scara Robot For Industrial Applications
As we know the workspace dimensions ie.
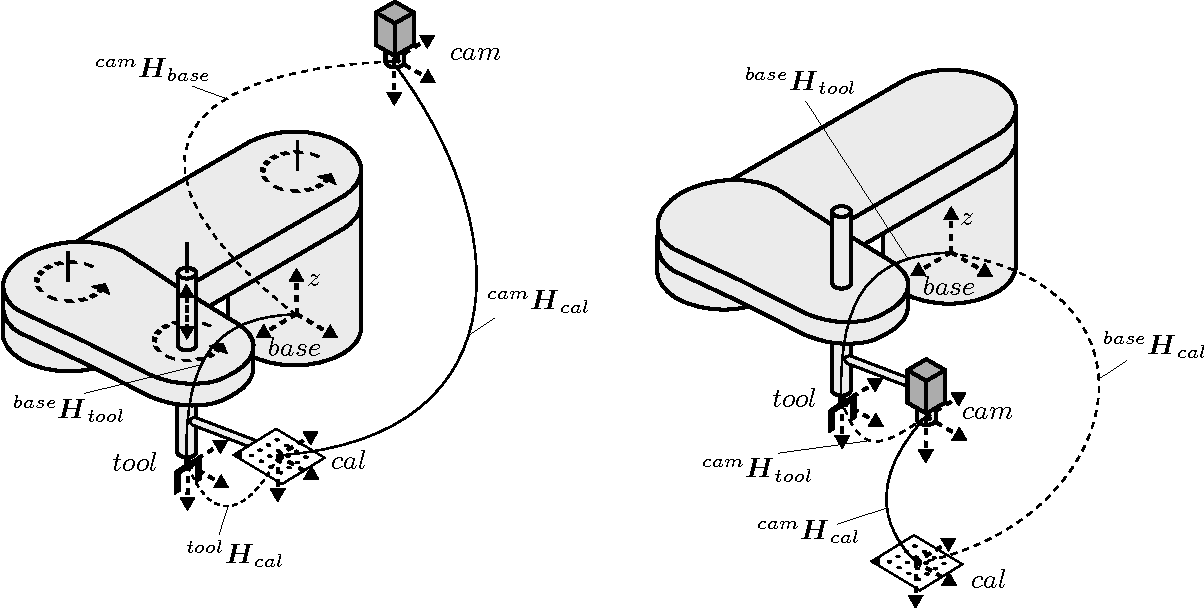
. The KR SCARA robot can be used across the entire temperature range between 5 and 40 Celsius IP protection class 20 Quick and easy integration Prepared ex works to integrate peripheral technology safely quickly and easily for minimal impact upon downtime and ease of integration into existing operational infrastructures. Firstly the SCARA robot is designed in accordance with the mechanical calculations. Off shelf parts are also.
SCARA robot is chosen after making concept evaluation in the conceptual design phase. The software is developed according to the obtained Cartesian velocities from joint velocities and joint velocities from Cartesian velocities. The maximum turning radius for second arm is 200 mm and the range of rotation movement is 1466.
125 SCARA Although originally designed specifically for assembly work these robots are now being used for welding drilling and soldering operations because of their repeatability and compactness. SCARA Robot is placed between center of workspace and it is kept away by 100 mm distance from the workspace. The SCARA Robot is designed for 1200500 mm workspace dimension.
However unlike the existing commercial robots the control architecture in FUM SCARA is designed to allow for. PROGRAMMING A SCARA ROBOT FOR A MANUFACTURING CELL TO ASSEMBLE AND PRODUCE MEDICAL DEVICES Abstract. The kinematic model is then built and the kinematic by using a Colour sensors interfaced with Arduino UNO analysis is performed based on.
1 Delta SCARA Robot DRS Series Current trends affecting manufacturing industries include labor shortage harsh environment short commodity cycles small-volume and large variety orders and frequent changeovers. This configuration flexibility allows such complex applications as spray painting and welding to be implemented successfully. Robots of this nature.
Delta SCARA Robot System User Manual SCARA CE Series 6 Definitions of stop Danger and Warning For your safety please read this manual before using the robot and have a clear understanding of all contents related to safety and warnings. Off shelf parts are also. 12 IR-820 fits in the smallest space.
Manufacturing cell operation depends on parts to be assembled. FUM SCARA robot offers impressive performance such as 001 mm repeatability maximum linear velocity of 85 ms in xy plane 05 seconds pick and place cycle time and a flexible control system. Stress analysis using finite element analysis is carried out before a prototype is developed.
Matlab-based Control of a SCARA Robot. Then forward and inverse kinematic equations of the robot are derived by using D-H parameters and analytical methods. Sample 3-FOUP Layout NOTE.
This research paper focuses on a single cell manufacturing machine setup that can be programmed according to requirements to perform certain processing functions. SCARA Robot Software-RS403 RS406 User Manual Original Instructions. Open the catalog to page 1.
Sample 2-FOUP Layout IR-820 can improve your footprint and reach higher throughput. The Scara robot is a variation of articulated robot-arms that are widely used in industries for applications ranging from welding painting assembly and pick and place. INDUSTRIE 40 Best Partner Multi-Axis Robot Pick-and-place Assembly Array and packaging Semiconductor Electro-Optical industry Automotive industry Food industry Articulated Robot Delta Robot SCARA Robot Wafer Robot Electric Gripper Integrated Electric Gripper Rotary Joint Single.
IR-820 SCARA 10 footprint shrinkage. The main reason for the popularity of industrial robots is the efficiency in doing repetitive tasks that would be otherwise monotonous and tedious work for a human being to carry out. SCARA robot is chosen after making concept evaluation in the conceptual design phase.
Then in third phase which is the product generation the chosen design of the SCARA robot is fine-tuned. The structure of the robot is firstly pre- In our SCARA robot is fully automaticThis can be done sented. When SCARA robots line up the maximum turning radius for first arm is 400 mm and the range of rotation movement is 130.
Higher reliability of SCARA robots belt-less transmission on XG series no electronic parts in movement Higher precision and high speed. Stress analysis using finite element analysis is carried out before a prototype is developed. When first arm reaches its limit second arm can move for other 100 to reach its limit.
We know the end determining the joint angles consider the motion of. Comprehensive line of YAMAHA SCARA robots P372 Orbit type Large type Arm length 700 mm to 1200 mm Maximum payload 20 kg. These specifications are in line with existing industrial robots.
The direct and inverse kinematics dynamics of the robot are then modeled. The assumptions made are. In response production lines.
High reliability is ensured by the simple mechanical structure of our SCARA robots that use a belt-less system in the XG series via a direct coupling between motors gearboxes arms and the shafts. This manual describes the SCARA Robot developed by HIWIN whose structure includes the body the control panel the Teaching Pendant optional the connection cable and the software. This masters thesis shows how it is possible to increase the flexibility and the functionality of a SCARA robot by introducing an interpreter in order to control the robot through Matlab a very versatile and powerful programming language.
Then in third phase which is the product generation the chosen design of the SCARA robot is fine-tuned. A user who purchases the robot can operate and maintain the robot via this manual. EFEM with SCARA Robot Minimal elbow motion required Space reduction PDO PDO EFEM with traditional R-theta Robot Minimum radius turning circle R-Theta vs.
The direct and inverse kinematics dynamics of the robot are then modeled.
Pdf Hand Eye Calibration Of Scara Robots Semantic Scholar
Pdf The Application Of Double Arms Scara Robot For Deburring Of Pcb Support Plate
Spt Rt6 602ss Epson T6 Scara Robots Scara T Series Scara Robots Robots Support Epson Us
Pdf Retrofitting Of An Ibm 7540 Scara Robot Sara Sobh Academia Edu
Pdf Modelling And Pid Control Of Scara Robot
Pdf Active Disturbance Rejection Control Of A Scara Robot Arm Semantic Scholar
Robotics Free Full Text Simulation Assessment Of The Performance Of A Redundant Scara Html
Design Construction And Control Of A Scara Manipulator With 6 Degrees Of Freedom Journal Of Applied Research And Technology Jart
Scara Robots Nordson Efd Pdf Catalogs Technical Documentation Brochure
Epson T Series Scara Robot Epson Robotic Solutions Pdf Catalogs Technical Documentation Brochure
Scara Robots Yamaha Motor Co Ltd Pdf Catalogs Technical Documentation Brochure
Spt Rls20 804st9p5 Epson Ls20 Scara Robots Scara Ls Series Scara Robots Robots Support Epson Us
Pdf Design Implementation And Control Of Scara Robot Ahmed S A L E H Ahmed Academia Edu
Dual Arm Scara Robot Duaro For The Food Industry Kawasaki Robotics Gmbh Pdf Catalogs Technical Documentation Brochure
Js3 Series Scara Robot Janome Industrial Equipment Pdf Catalogs Technical Documentation Brochure
Pdf Modelling And Control Of A Scara Robot Using Quantitative Feedback Theory Semantic Scholar
Scara Robot Report Pdf Real Time Computing Operating System
Jsr4400n Series Scara Robot Janome Industrial Equipment Pdf Catalogs Technical Documentation Brochure
Scara Robotic Arm Googol Technology Hk Limited Pdf Catalogs Technical Documentation Brochure
Comments
Post a Comment